Client: Third Dimension
Vacuum casting, using silicone elastomers and polyurethane resins plays a major part in the production of this rugged, hand-held laser measuring gauge, which has been a long term, batch-run product manufactured by Amalgam for Third Dimension, a world leader in non-contact optical metrology solutions.
Utilising our extensive vacuum casting facilities and a broad range of knowledge related to polyurethane resins and silicone elastomers , we have been able to constantly revise and develop the Gap Gun’s outer casing and range of peripherals to better meet the end users needs. New connection ports have been added, cutting edge high impact resins implemented and a cost efficient value range introduced.
Although primarily intended for prototyping, vacuum casting has also proved perfect for the varying requirements of several end users. The relatively low cost of tooling allows viable production runs as low as 20 units, feasibly permitting specialist designs and modifications to each run.
The core Gap Gun has recently been hard tooled and is now injection moulded in the UK. However this is not the end of the story; as there are many mating components, to name a few: overmoulded standoffs, aluminium laser heads and light shields, not to mention new internal components, and the silicon protective jacket we continue to produce.
An overview of the Vacuum Casting Process
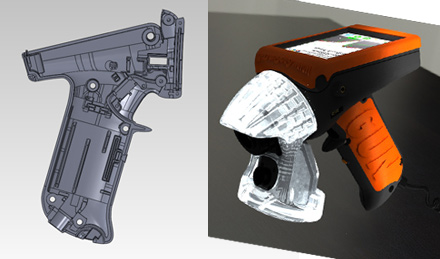
Within rapid prototyping, various processes exist to translate an image on a screen into a physical model. We primarily use the SLA process to create master models although many other additive manufacturing processes, CNC machining and even handmade masters are also commonly used. While these new technologies allow incredibly complex and high-tolerance shapes to be created, they are by no means clean processes and the objects they create still need a great deal of skill and hand-finishing to bring them up to a desired standard. Many different finishes can be achieved; matt, gloss, satin, and the characteristic ‘spark’ finish of a part that has been injection moulded. Once cleaned up and finished, the casting master is ready for tooling.
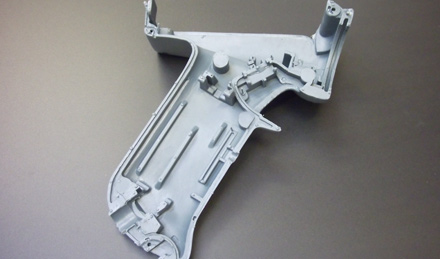
Mould-making, or tooling, is a process where the casting master is suspended in a box, with risers and runner branching off it to create channels through which residual and reaction gases can escape when the part is cast. Liquid silicon is carefully introduced under vacuum, capturing the surface texture perfectly. The tool is then placed in a vacuum chamber, removing any trapped air or bubbles, which would otherwise create voids in the tool that could potentially deform the surface of a tolerance part. The tool is then placed in a temperature controlled oven for curing. Once cured, the silicon block is split open, and the master removed, leaving the negative space of the master within it.
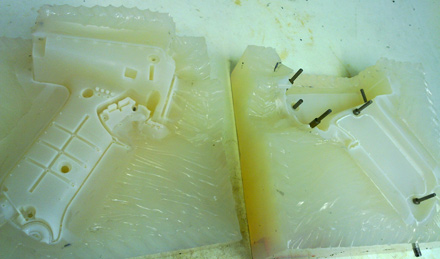
We use various polyurethane resin systems for vacuum casting and rapid prototyping – these systems can mimic almost any industrial method of production, meaning we are able to produce realistic components affordably, in small quantities. The liquid resin is poured into the tool, which is placed in a temperature controlled oven for curing. Once cured, the tool is split, revealing the cast part.
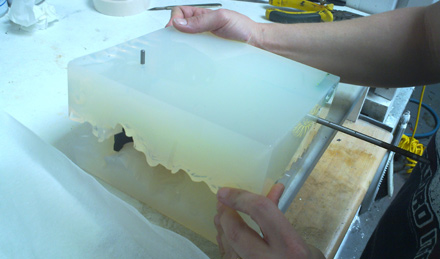
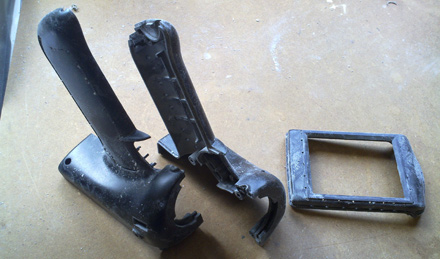
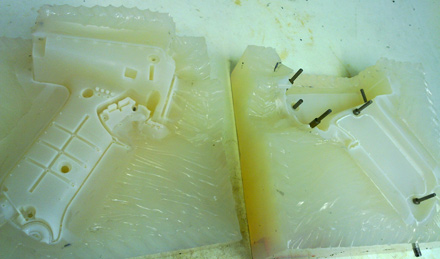
The cast is then meticulously cleaned up to become a finished component. A micron-thin seam of excess material, known as ‘flash,’ occurs where the two halves of the tool meet; this must be gently cleaned away. The risers and runners are snapped off and sanded away.
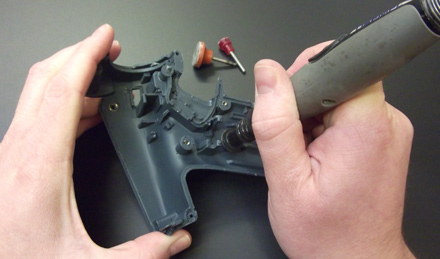
The rubberised parts of the design are ‘overmoulded’, which can be achieved in various ways. Two versions of the same tool are created and tooled, one without the overmoulded component (tool A) and one with (B). The cast from tool A is placed inside tool B, and a different material poured in, filling the new spaces. This method allows us to achieve a range of effects, for example soft rubber grips perfectly moulded over hard handle parts. Alternatively, overmoulded components can be made separately and attached afterwards, saving on production costs and time, a process used for the Gap Guns. The suitability of these each of these processes depends on the nature of the part and the level of finish.
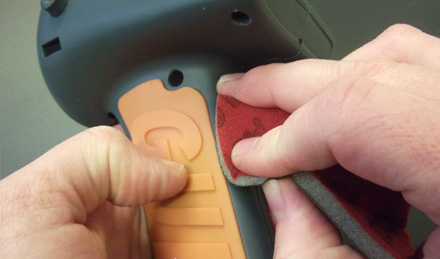