Client: Jon Rathbone
When potty training their children, Jon & Lucy Rathbone found that every potty they tried would allow the contents to dribble over the sitting area and sides when being emptied. This got them thinking about what features would make for a “better” potty. Shortly afterwards Jon approached Amalgam with a request to develop his innovative ‘Pourty’ potty design into a working model.
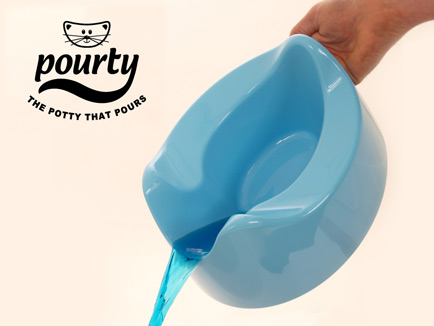
Visit the Pourty website or have a look at the product demonstration video.
Product Development
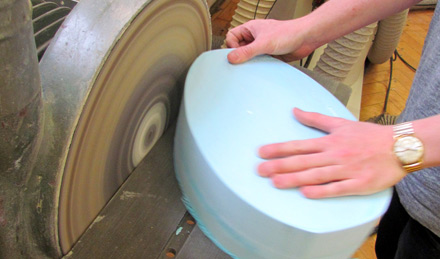
After an initial meeting we hand produced a bluefoam model, which was gradually refined to get as close as possible to Jon’s list of desirable features. Once he was happy with the foam model, our in-house designers digitally scanned the shape then reverse engineered to create 3D CAD data. This was used to produce an SLA prototype for “wet” testing, and a few more final adjustments were made to both the CAD and the master model to ensure perfect pouring.
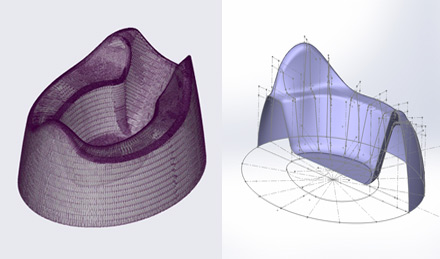
The final stage was then to create several self coloured vacuum cast versions. This involved creating a huge silicone mold, one of the largest we had made to date.
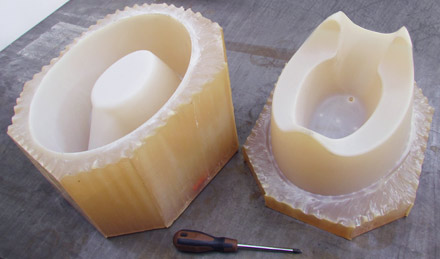
The final cast prototypes were ready to be ‘live tested’ and used as marketing tools for this exciting new product. We put Jon in touch with a trusted Far-Eastern manufacturer who, following successful negotiations, took on the job of hard tooling and producing the Pourty. Our 3D CAD files were produced in Solidworks, and as such were completely compatible with every stage of the process and obviously saved Jon a lot of time and money.
The Pourty potty won Best New Product to Market 2010/11 and is consistently rated 5/5 in potty reviews for quality, value for money and ease of use. It has gone on to be stocked world-wide by the vast majority of high street retailers. Jon, meanwhile, has given up the day job and is not only realising his dream but also training a third child – using Pourty of course!