Meet Mike Quarry, one of Amalgam’s engineers working on all sorts of projects. He’s been…
Development of the Holovis game controller for immersive 3D experience
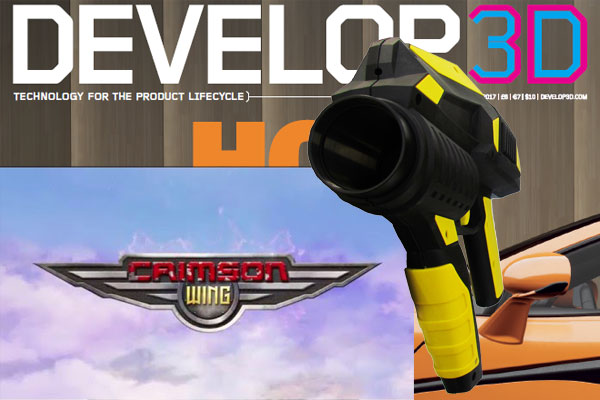
Published in this month’s Develop 3D, you can take a look behind the scenes at the development work we did for Holovis to design and manufacture the Crimson Wing game controller.
Holovis came to Amalgam with a basic outline shape developed as a 3D concept. Their first priority was to develop the ergonomics, starting with the handle of the controller. To test each handle design, we made controller handles out of modelling foam, using our 3-axis CNC machine. Once we determined the desired shape and best size, we adjusted our CAD model and applied finer exterior design details to it.
The concept version was then shelled out, for us to apply all the required internal features and electronic support bosses. The next stage was to develop our CAD file into a final design, which took four weeks of computer-aided design work.
Once the CAD files were complete, we 3D printed a set of parts, then finished and assembled them ready for use as vacuum casting masters. Our vacuum casting process produces strong, realistic and functional plastic prototypes, so we can deliver short-run production items like these for a wide range of industries and clients.
From there we produced a set of soft tools and a small batch of game controller casings, then fitted the electronics inside, ready for the launch of the new game, Crimson Wing. The batch of prototype controllers was used successfully at the launch during IAAPA Expo in November 2015.
Since the IAAPA show, Holovis published their Extended Preview video showing how excited the audience were, highlighting the power of virtual reality. Using their technology, Holovis creates highly immersive sensory experiences, which are becoming massively popular for visitor attractions, theme park rides and museums.